7年研究、7年建设,24公里、超1.5万名建设者……横跨伶仃洋、联通大湾区的超级工程深中通道,即将改变珠江口的未来。日前,深中通道管理中心对外公布,这个世界首例集“桥-岛-隧-水下互通”四位一体跨海集群工程,已形成了10项国际领先技术,并创造了10项世界之最。
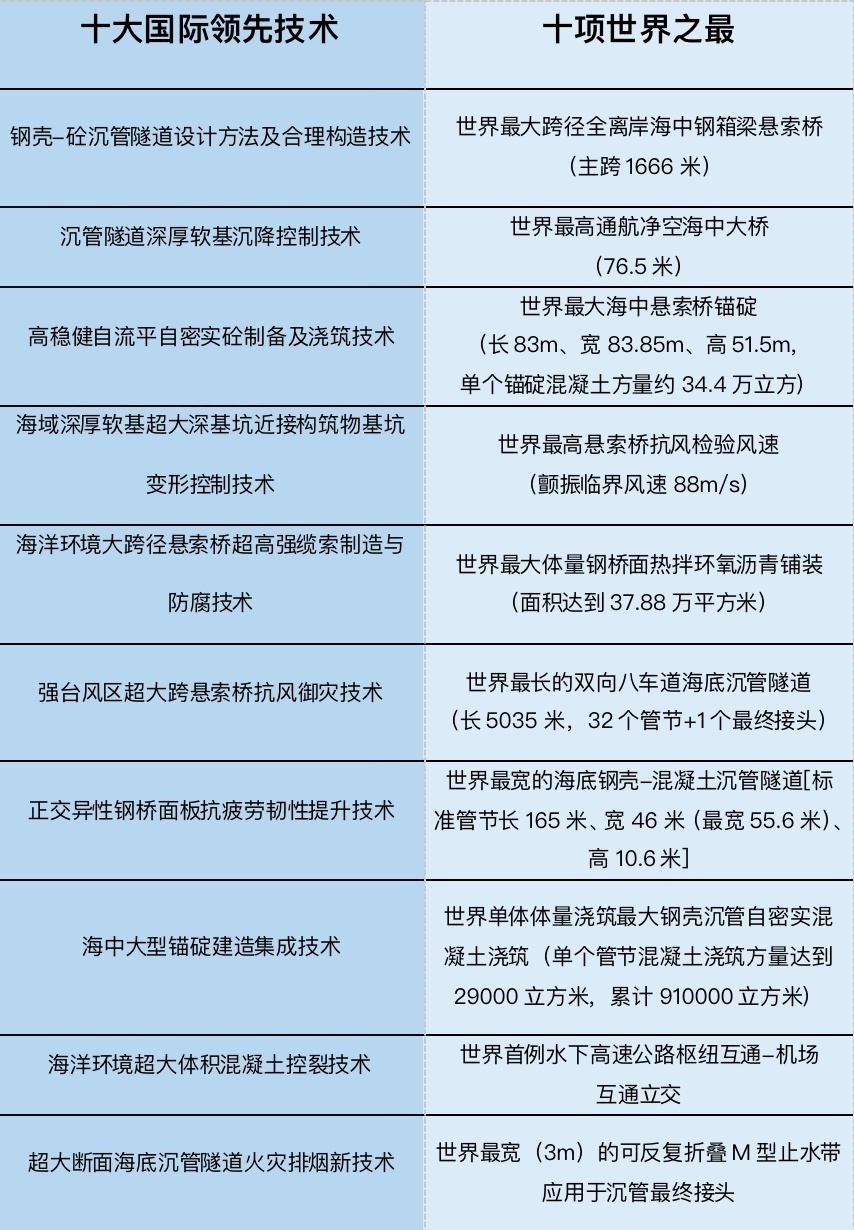
“这10项‘国际领先技术’里面,就凝结了来自我们沉管隧道建设者的卓越智慧和辛勤汗水。”中交四航局深中通道项目负责人张文森欣慰地说。
沉管隧道段作为深中通道的核心控制性工程,沉管的预制质量直接决定了100年使用寿命的实现。实际上,由中交四航局深中通道项目团队在钢壳-混凝土沉管隧道设计施工领域形成的原创性成果,在这“10项”里排名榜首,为“0-1”的创新性突破。
他们用人工智能和新装备、新科技攻克了深中通道项目中世界首例特长双向八车道钢壳混凝土沉管隧道的技术难题,完成了23节单节重达八万吨沉管的预制(含最终接头)。因此,今年5月,国际隧协授予深中通道“全球隧道与地下工程领域50项标志性工程”称号,为世界跨海通道工程贡献了中国方案。
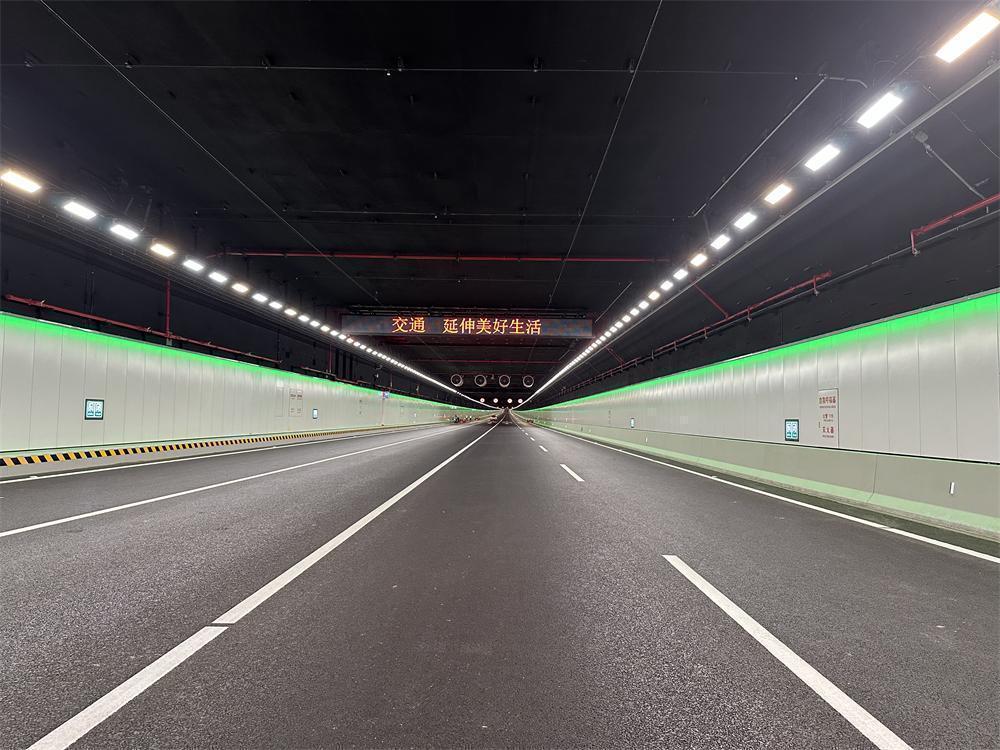
沉管隧道段是整个工程中技术含量最高、难度最大的控制性环节。2018年,这个艰巨的任务,又落在曾完成港珠澳大桥沉管预制工作的中交四航局肩上。
“我们在港珠澳大桥沉管建设理念‘每一节都是第一节’的基础上,根据深中通道钢壳沉管特点,进一步提出‘每一个仓格都是第一个仓格’的理念,持续强化全体建设者的质量意识,确保每个标准管节的2255个仓格都能精准浇筑、丝毫不差。”说这话的张文森,几乎参与了港珠澳大桥和深中通道两大超级工程的沉管建设全过程。项目团队还以中交集团平安百年品质工程创建为载体,将质量第一的理念贯穿到项目班子、职工和全体协作队伍,增强全员质量创新能力,全面提升工程质量。
深中通道单个标准管节长165米、宽46米、高10.6米,浇筑完成后重达80000吨。这么个“巨无霸”在出运安装前需要涉及多次转运,哪怕出现一毫米的偏差,都有可能变形损坏,对工程工期、质量造成不可估量的影响。
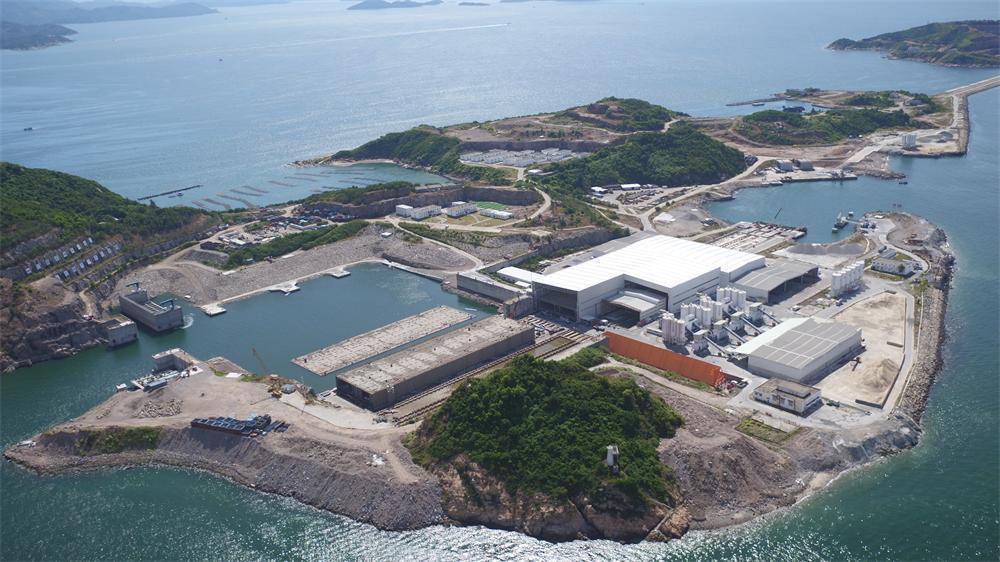
在沉管预制过程中,项目团队每个人都在平凡的岗位做着不平凡的事情。每次钢壳沉管移运上岛,项目质检部部长邓军都要带团队对管节的隐蔽仓格进行检查验收。到仓格浇筑前,他还要俯身用探照灯认真检查每一个仓格内部的结构,确认是否有杂物、积水,并做好记录,如此循环往复,直至检查完2000多个仓格。
测量班就是项目团队观察沉管变化的火眼金睛。“我们会从沉管上岛开始,对浇筑前、浇筑过程中和浇筑后的管节变化全程密切跟进,精准测量,把好每一道工序的‘数据关’。”测量班部长周俊文介绍道。除了细心,测量团队还要有强大的耐心和定力。不管白天黑夜,无论日晒雨淋,他们都要坚守在现场,紧紧盯着仪器上的数据变化,随时与设备部团队沟通同步管节移动的情况,确保管节安全稳定。
“经过5年多的努力,我们完成23个管节预制,共51286个仓格的浇筑,实现脱空监测合格率100%,得到了业主的高度认可。”回望这几年的艰辛,张文森认为一切都是值得的,“我们兑现了要做最好沉管的承诺。”
深中通道沉管段是在世界范围内首次大规模采用钢壳混凝土结构,于国内则是全新的结构和技术。面对前所未有的挑战,中交四航局建设团队坚持直面世界科技前沿、直面国家重大需求、直面经济主战场,激发广大员工科研创新活力,将预制厂打造成为科技创新的孵化基地,自主研发了高体积稳定性自密实混凝土、世界最大智能台车编队、国内首套智能浇筑设备和“四航固基”号DCM船等技术、装备,系统解决了8万吨沉管快速移运和自密实混凝土浇筑的百年质量难题,彰显出“中国智造”“中交品牌”实力和影响力。
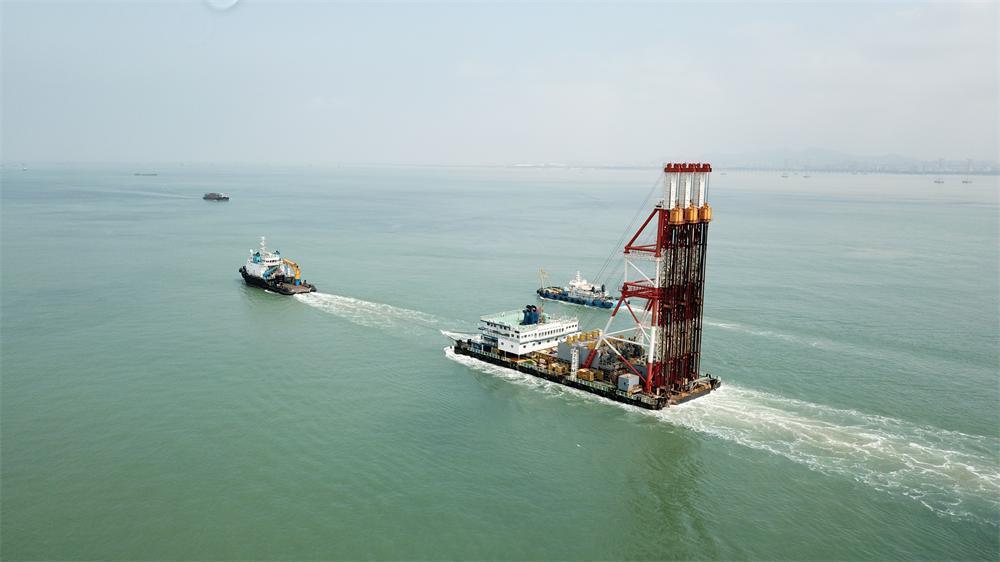
早在2015年,为直观获取混凝土在钢模中的流动状态,广东省交通集团、深中通道管理中心和中交四航局就组成技术专家攻关小组。历时4年多,在实践中研究出了能满足钢壳质量标准的混凝土材料,突破了封闭式隔仓混凝土填充密实度等“卡脖子”难题。
“光是为了找到最好的原材料,我们就跑遍了这方圆数千公里,晚上做梦都是混凝土。”时任中交四航局深中通道项目试验室主管孙帅说道,“解决了影响混凝土性能的单个敏感因素后,还要继续研究温度、时间、浇筑泵管、设计性能指标等多个因素耦合下对混凝土的影响,必须确保混凝土性能万无一失。”在试验了300多方混凝土之后,试验团队终于找到了最合适的配比,制作出高流动性自密实混凝土,在足尺模型试验的脱空检测中,达到了设计要求,脱空率控制在了5毫米以下。在首个管节浇筑完成的脱空检测结果中,每个仓格的混凝土脱空率都稳定在了2—3毫米之间,是百年工程品质保证的首个屏障。
面对传统浇筑设备适用性差、沉管预制工期紧和人为因素影响等问题,中交四航局技术团队整合工程和机械的的技术资源,自行设计一款智能化浇筑装备,具有越障能力,可灵活移动,还能实现浇筑速度、下料高度等因素的稳定控制,精细化控制每个仓格的混凝土饱满度,为沉管预制的质量和效率提供了可靠保障。
港珠澳大桥建设期间,中交四航局项目团队创造了8万吨沉管7天移运的纪录,而深中通道的工期对沉管“智”造效率提出了更高的要求。在比选了十多种移运方案后,项目最终决定研发智能台车。智能台车的研发横跨十几个学科,涉及上百个课题。“我们接连找了业内共11家高规格、实力雄厚的设备制造商,但由于项目规模大、难度高、技术复杂,没有一家单位能保证完成,我们便决定自主研发。”中交四航局技术中心总经理陈伟彬带领团队将智能台车研发的使命扛在了自己肩上。项目团队数十次外出求学、上千次的验算、失败、重来,经过两年多的攻坚,终于成功研发出了世界最大智能台车编队,实现了沉管移运从7天到3个小时的巨大飞跃,为行业超大型构建移动提供了更优解决方案。
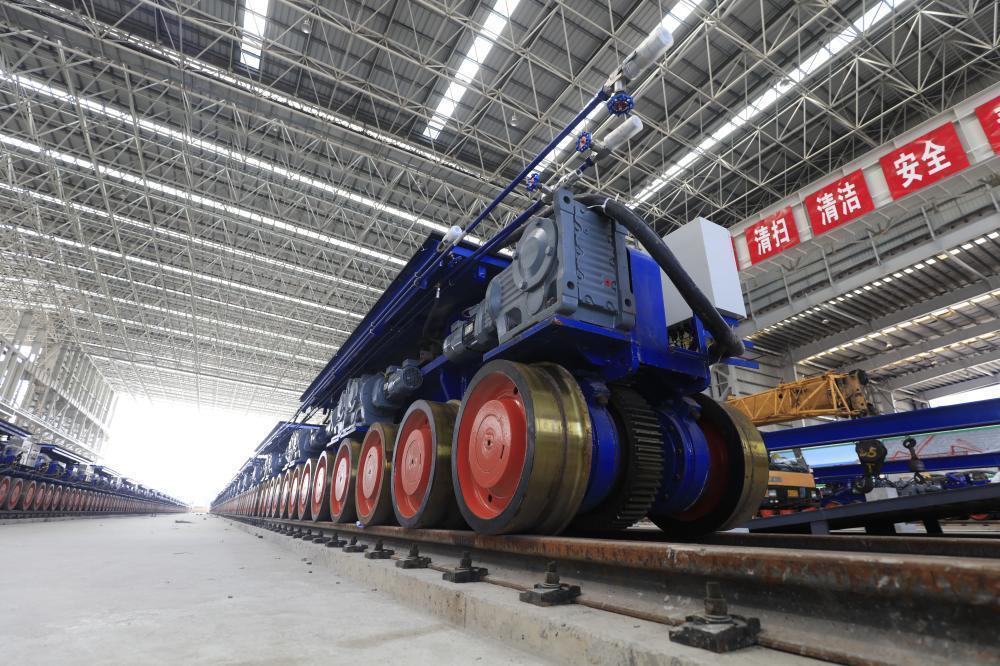
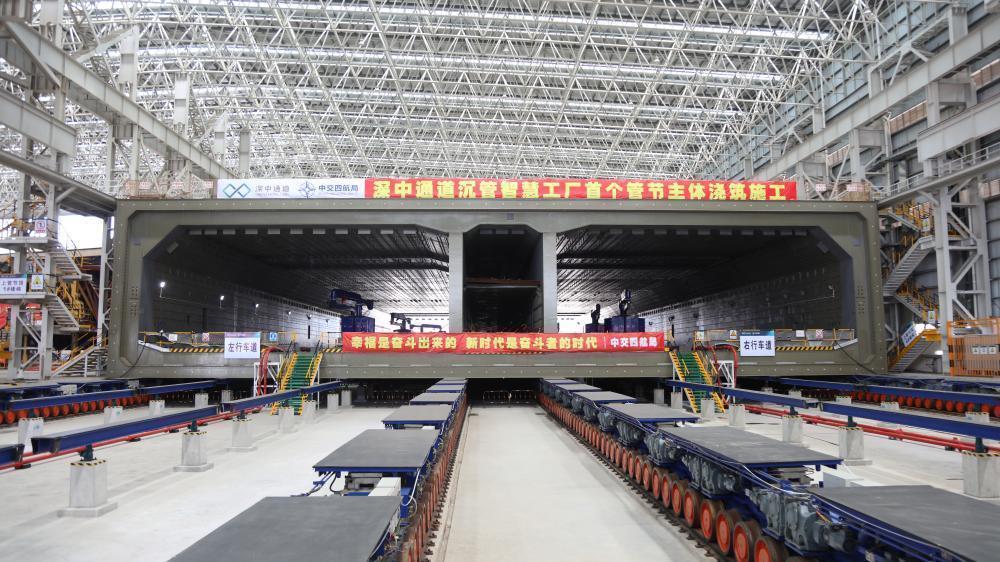
5年多的光阴,智能台车在牛头岛沉管预制生产线个管节从卸驳区驮运到浇筑区,智能浇筑设备把约70万立方米的自密实混凝土精准泵送到沉管的每一个仓格,每个生产工序紧密衔接,流水线式标准化作业,沉管“智”造助力深中通道建设全面提速。
中交四航局深中通道沉管智慧梦工厂位于珠海市牛头岛,这里是人民海军第一战——万山海战的主战场之一,也是港珠澳大桥沉管建设的基地。中交四航局项目党支部传承和弘扬港珠澳大桥精神,以高质量党建引领项目高质量管理,以智慧工厂为着力点,将项目所在的沉管预制厂打造成为具有“创新、品质、绿色、幸福、强国”五大特点的梦工厂,为建世界一流可持续跨海通道,打造珠江口百年门户工程贡献中交四航局的磅礴力量。
在深中通道建设过程中,中交四航局项目党支部激励全体员工扛起时代使命,全力攻克沉管隧道建设核心技术,解决“卡脖子”难题。以党员为核心的建设团队坚持自主创新,相继攻克了沉管预制关键技术和装备难题,并日复一日、持之以恒地抓好沉管预制质量,完成所有施工任务。项目党支部以“绿色智造”为主线,以技术创新为依托,在工程建设过程中,将白海豚保护列入施工策划、船舶施工设计、环保监管机制等各项设计、制度中,发明了一项国家实用新型专利——深层水泥搅拌船用整船防污系统,以实际行动筑牢绿色发展安全屏障,为海洋施工生态保护进行了有益探索。项目党支部牢牢站稳人民立场,坚持做人心工程,通过打造世界首个沉管领域的产业工人培训基地,持续提升工人业务能力,助力拓宽职业发展渠道,增强就业竞争力。
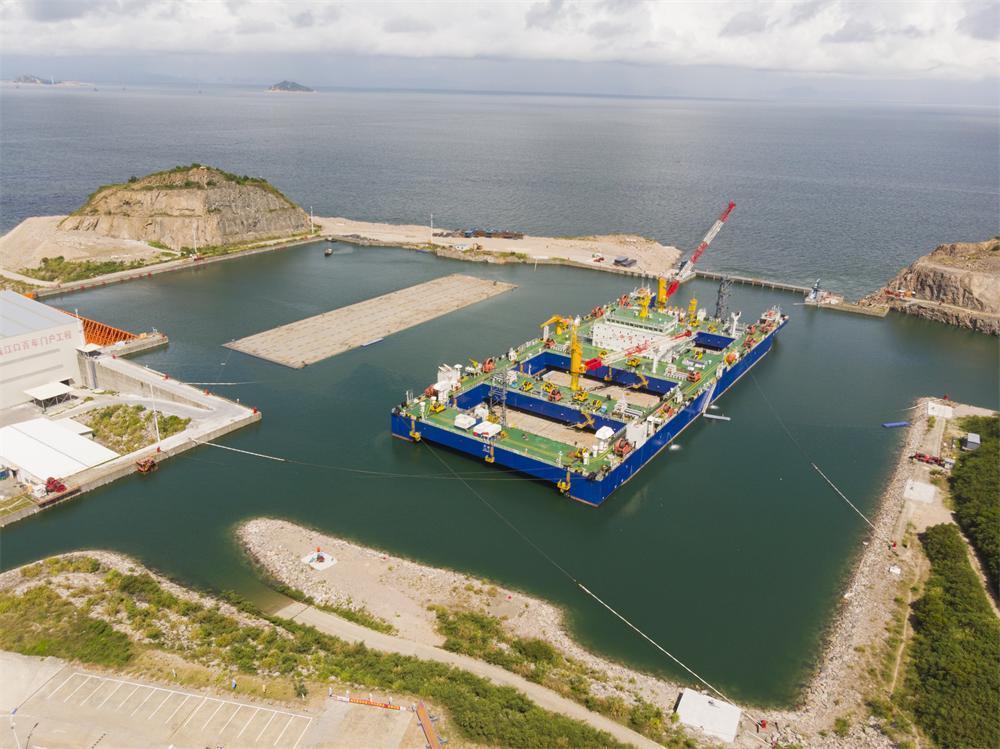
项目党支部高度重视品牌塑造,以沉管造型为框架,创造性设计打造出展现我国在跨海通道建设领域技术储备和能力的牛头岛展厅。自开馆以来,年均接待外来客人上百批次,年均客流量近万人。“牛头岛展厅展示深中通道和港珠澳大桥沉管隧道建设成果,我们希望更多的人能了解沉管隧道这种建设模式,了解中国建设者攀登交通技术高峰的奋斗历程。”有时候一天会连续接待四五波外来参观的团队,频繁的接待让项目党支部杨昆应接不暇,他笑言这是甜蜜的烦恼。
得益于“五个梦工厂”党建品牌的建设,中交四航局深中通道预制基地成为中央驻港联络办广东联络部爱国主义教育基地的组成部分,并正式挂牌澳门中联办培训中心现场教学基地,成为广东省国资委党委“双区建设、国企担当”党史学习教育现场教学培训点,展现了新时代中国在跨海通道领域取得的辉煌成就,逐步成为社会各界了解国家基础设施前沿科技的窗口,极大地提升了参观者的国家荣誉感和民族自豪感。